Making Concrete More Durable: Tips and Techniques
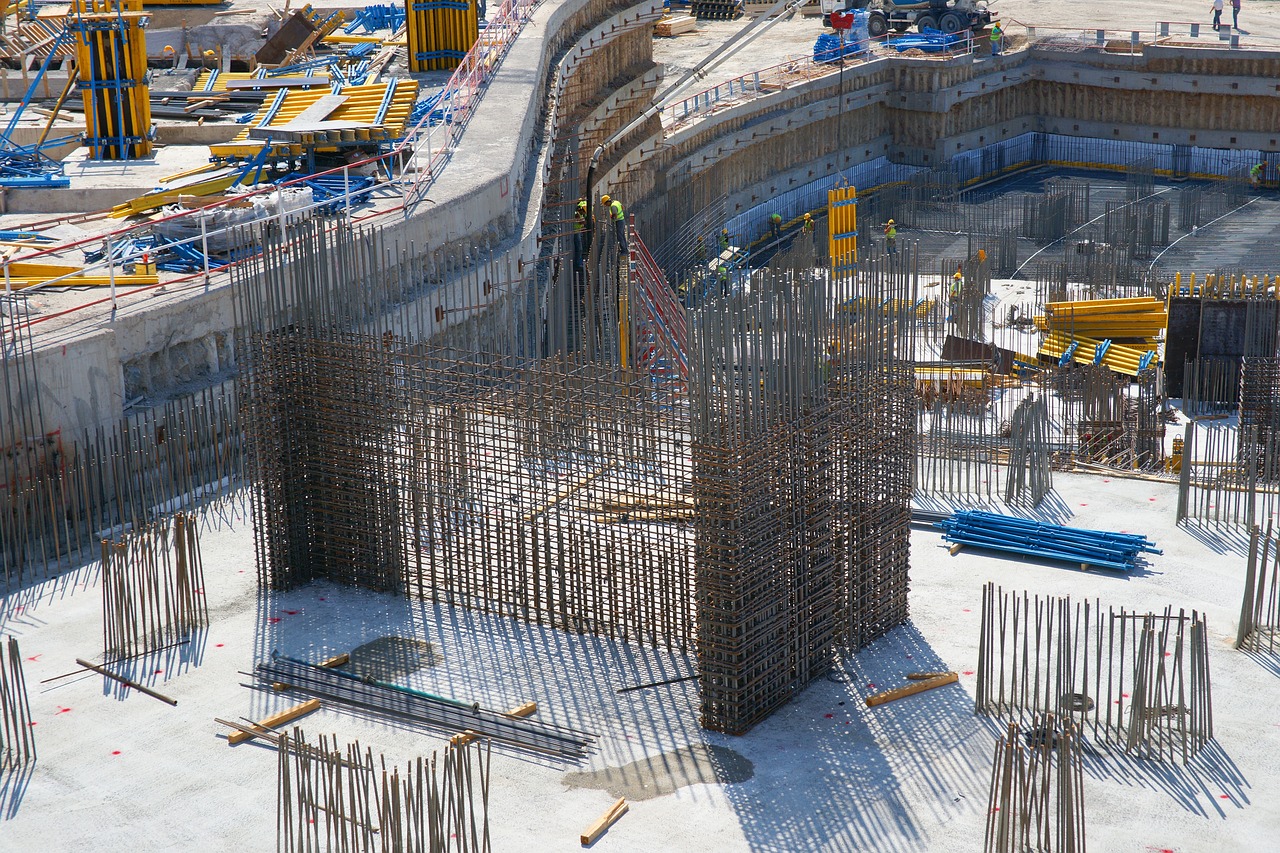
In the past, concrete was the preferred building material of the Roman Empire and was used to build wharves, breakwaters, and other harbor structures in addition to monuments like Rome’s Pantheon. It makes sense that concrete buildings are designed to last a lifetime. Concrete structures typically have a 50–100 year design life, but sadly, a lot of the buildings built today fall short of expectations. Saying that practically all of the negative things that happen to concrete are caused by water is not an exaggeration. Chemical pollutants that are carried into the concrete by water can erode the surface, expand the concrete, and corrode the steel reinforcement. The following five recommendations will help you prolong the life of your concrete and prevent premature deterioration of concrete infrastructure:
Blending Style
The foundation of durability is a concrete mix design appropriate for the service conditions to which the concrete will be subjected. Perhaps the most crucial element of the mix design is the amount of water specified. For concrete that is regularly exposed to extreme conditions, a low water-to-cement ratio of 0.40 to 0.50 is typically advised. Don’t top off the water on the spot. More water will make the material less strong, more permeabile, and more likely to scale.
One mix design cannot be long-lasting in every circumstance. For instance, when concrete is exposed to sulphate-contaminated soil, the mix design should take into account the use of sulphate-resistant cement. However, when a concrete structure is subjected to freezing and thawing cycles in a damp environment, this mix design is inappropriate. Given that entrained air will help to protect the concrete in these circumstances, an air-entraining admixture should be included in the mix design in this instance.
Water-reducing admixtures increase the degree of cement hydration and decrease the amount of water needed for a given consistency, which results in a cement paste that is more resilient. Concrete that has been hydrated more thoroughly is more resilient.
The aggregates are other key elements of the mix design. Pop-outs or alkali silica reactivity (ASR) can result from contaminated aggregates, and uneven setting times in off-spec cement can cause finishing issues.
Building Joints
Water will frequently find its way into and through construction joints, which are a common weak point in the structure. Your structure may sustain damage from the reinforcing steel corroding due to water seeping through the joints. To prevent random cracking, make sure to design your structure with sufficient, predetermined control joint locations. Additionally, ensure that each joint has its own effective waterproofing system. A joint waterproofing system with crystalline technology offers the best long-term protection at joint locations because it self-seals random cracks, adding extra reliability and protection.
Stop Early Moisture Loss While Placing
Maintaining the proper hydration of the cement for maximum strength, increased density, decreased permeability, and increased resistance to scaling is facilitated by keeping the concrete moist and at a suitable temperature. Appropriate placement and finishing are necessary for durable concrete because overly aggressive or hurried finishing causes blistering, lowers surface air content, and compromises durability. When troweling concrete, it is common practice to “bless” the surface with water, which raises the risk of surface scaling and spalling. The concrete in the near-surface wear zone becomes weaker as the water-to-cement ratio rises at the surface. “Blessing” may not be necessary in situations involving rapid moisture loss if an evaporation retardant is used. This will increase the productivity of the placement crew, improve the overall quality of the concrete, and prevent surface crusting and plastic shrinkage cracking, all while lowering overall placement costs.
Minimal Permeability
All good concrete has one thing in common: low permeability. You may need to modify the mix designs to suit the conditions. Reducing the amount of free water in your mix and using plasticizers or admixtures that reduce water content are crucial for achieving proper mix proportioning and decreased permeability. Concrete should have a waterproofing admixture applied to prevent water intrusion.
Appropriate Curing
The key to extending the life of your concrete is curing, which is keeping the environment conducive to the concrete’s ideal hardening and strength-gain. Most crucial are the right humidity and temperature. In order for strength development to proceed at a reasonable pace, the temperature needs to be higher than 10°C. Maintaining moisture is essential to promoting cement hydration and preventing drying, shrinking, and cracking of the concrete, especially in the initial days.
After Curing, Keep Concrete Safe From De-icing Salts
In the early stages of concrete’s life, frequent wetting and drying will result in crazing, scaling, decreased concrete strength, and an increased risk of scaling. During the first few days of hydration, when its high moisture content and low strength make it most vulnerable to freeze/thaw damage, concrete must be shielded from freezing temperatures. If the deicer agent presence is unavoidable, apply a surface treatment such as Aquapel to effectively repel a significant portion of the moisture that will lead to deterioration and stop almost 90% of the deicer salts from migrating.
Placement of Concrete
It is imperative that concrete be properly placed and compacted into a solid mass devoid of any crevices or pockets of rock. Most frequently, voids appear behind or beneath reinforcing steel bars, particularly in locations where numerous bars are grouped together. Make sure all concrete is adequately vibrated, paying close attention to any crowded reinforcement. Where there is insufficient cement paste and fine aggregate to fill the void left by large aggregate, there are rock pockets. Prior to pouring concrete, make sure there is no standing water and avoid moving the concrete too far from its original location. The majority of these worries can be reduced by using self-consolidating concrete.
Concrete structures can be made to last a long time by using appropriate mix design, permeability reduction, and careful jointing, placing, and curing procedures. These actions will prevent corrosive conditions and other deteriorating mechanisms from developing.