26 Types of Concrete
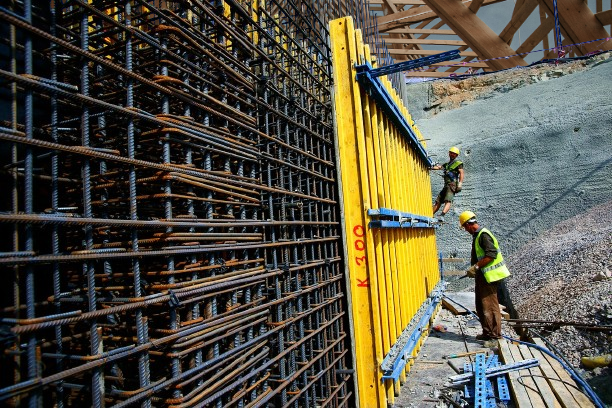
Concrete can be found practically everywhere, including in buildings, bridges, walls, floors, patios, roads, swimming pools, and even cement houses. These structures are all dependent on a synthetic material with an easy-to-follow formula. How is so much concrete produced?
Cement, water, and coarse aggregates make up concrete. They combine to form a building material that solidifies with time. Concrete’s characteristics, such as these, depend on the amount of cement and water used.
- Power
- Sturdiness
- Deficiency against radiation or heat
- Adaptability
There are countless uses for freshly laid concrete. It can be cast and poured into a variety of shapes, including circles, squares, and rectangles. It can also be applied to other common structures like lentils, doors, beams, columns, and staircases. Different grades of concrete, such as normal, standard, and high-strength, are produced. These grades show what kinds of construction applications and pressure levels the concrete can withstand.
Which kind are you in need of? Depending on the needs of your project, our guide can assist you in making a decision.
How Is Concrete Made?
Regardless of the purpose for which you intend to use concrete, achieving the desired quality requires proper mixing ratios. To make concrete, you can use two different mixes:
- Nominal mix: Small residential buildings and other common construction projects use this mix. A 1:2:4 ratio is used in the majority of nominal mixes. The ratio of cement is represented by the first number, the ratio of sand by the second, and the ratio of aggregate required based on the weight or volume of materials is represented by the third.
- Design mix: To ascertain the mixture’s compressive strength, laboratory testing is used to determine the final proportions for the design mix, also known as the mix design. Based on the concrete component’s structural design, this will establish the required strength.
In addition to the mix proportions, the concrete is mixed using one of two methods:
- Machine mixing: Various kinds of machines are used in this. After adding the ingredients to the machine, they are mixed. New concrete is the end product.
- Hand mixing: On a level surface, the ingredients are combined by hand. After that, employees use specialized instruments made just for the job to manually mix the cement with water.
The type of concrete you want will determine how much and what kind of mixing you use.
The 26 Different Concrete Types
Concrete comes in a wide variety of varieties, some of which are suitable for similar applications. Depending on the objective you hope to accomplish. You can select the right type of concrete to complete the job.
- 1. Concrete of Normal Strength
In a 1:2:4 ratio, aggregate, concrete, and sand are the main ingredients that go into making normal strength concrete. This mixture yields concrete with a normal strength that is suitable for a wide range of uses. It takes anywhere from thirty to ninety minutes to set, depending on the cement’s characteristics and the local weather at the concrete site.
It is typically applied to buildings or pavements where high tensile strength is not required. Since it is not very good at withstanding the stresses caused by vibrations or wind loading, it is not very good for many other structures.
- 2. Concrete Reinforced
In contemporary construction and industry, this type of concrete is frequently utilized. The steel rods, cables, or wires that are inserted into the concrete before it solidifies give reinforced concrete its strength. Rebar is a more common term for these products. Fibers have recently been added to this concrete to strengthen it.
To prevent breaking or cracking, these reinforcements are resistant to tensile forces. To support a lot of weight, the concrete itself resists compressive forces. When combined, the two materials form a robust barrier against a variety of applied forces, including those from cars. They essentially merge into one structural component.
It was developed in the 19th century and had a significant impact on the construction sector. Reinforced concrete is needed for bridges, buildings, and roadways. The likelihood is that you will see reinforced concrete with rebar the next time you visit a construction site.
- 3. Simple or Typical Concrete
This concrete also contains cement, sand, and aggregates and is mixed according to the standard 1:2:4 ratio. It can be used to construct buildings or pavement in applications where tensile strength is not a critical requirement. It experiences the same problems as regular strength concrete, namely poor resistance to wind loading and vibrations. In the construction of dams, plain or ordinary concrete is also utilized. This particular type of concrete has an extremely good durability rating.
- 4. Concrete Prestressed
Large-scale concrete projects frequently employ prestretched concrete units. A specific method is needed to make prestressed concrete. It has bars or tendons, just like reinforced concrete does. However, stress is applied to these bars or tendons prior to the concrete actually being applied.
These bars are positioned at both ends of the structural unit where they will be utilized after the concrete has been mixed and poured. This unit is compressed once the concrete hardens.
The unit’s lower section becomes stronger and more resilient to tensile forces as a result of this compression. But heavy machinery and skilled labor are needed for this process. Prestressed units are typically made and put together on location. Bridges, heavy-duty buildings, and long-span roofs are constructed with prestretched concrete.
- 5. Precast Concrete
Precast concrete needs to be manufactured and cast in accordance with precise measurements, just like most other classes of concrete. Eventually, these concrete units are delivered to the application site, where they are assembled for usage.
When you travel on highways, you frequently witness these units being transported to work sites. Uses for precast concrete include:
- Blocks of concrete
- Precast walls
- Units for stairs
- Poles
Precast concrete has the benefit of quick assembly. The units are of extremely high quality because they are produced in a factory.
- 6. Concrete that is lightweight
Any type of concrete with a density of less than 1920 kg/m3 is considered lightweight. Lightweight aggregates are used to make lightweight concrete. One ingredient that increases the density of a concrete style is aggregate. The different natural, synthetic, and processed materials that make up these lightweight aggregates include:
- Clays
- Enlarged shales
- Scoria
- Pumice
- Lite
- Vermiculite
The low thermal conductivity of lightweight concrete is its most significant characteristic. Lightweight concrete is frequently used to make building blocks and long-spanning bridge decks. Steel structures can also be safeguarded with its help.
- 7. Superior Quality Concrete
High-density concrete serves a very particular function. It is widely employed in the building of nuclear power facilities. High-density concrete’s heavyweight aggregates aid in the structure’s resistance to radiation.
Usually, crushed rocks are utilized. The most common crushed rock used is barytes, a colorless or white substance made mostly of barium sulfate, which is the main ingredient in barium.
- 8. Concrete that has been stamped
Stamped concrete, also referred to as textured or imprinted concrete, is made to accurately mimic the pattern and appearance of real stones, tiles, bricks, and granites. Stamped concrete is frequently used to build driveways, interior floors, patios, and pool decks.
To achieve this look, impressions are made on the concrete’s surface using expert stamping pads. You can also use different coloring stains and texture work to achieve a natural finish.
The following are a few benefits of stamped concrete:
- Cost-effectiveness in contrast to natural stone and pavers
- Simple upkeep after sealing
- Becomes non-skid when a non-skid additive is added.
- Improves outdoor area and raises its worth
- Robust and long-lasting
- Extensive use of pattern and color
- 9. Concrete with Air Entrained
Every cubic foot of certain types of concrete contains billions of microscopic air cells. The concrete’s internal pressure is released by these tiny air pockets. They offer minuscule spaces for ice-forming water to expand.
During the mixing process, a number of foaming agents are added to the concrete to entrain the air, including:
- Acids fatty
- Resins
- Alcoholics
Because this concrete is mixed on the application site, careful engineering supervision is needed during the mixing and entraining process. Approximately 3% to 6% of the concrete’s volume is made up of the entrained air. Nearly all concrete used in freeze-thaw cycles or in frigid climates is air-entrained.
- 10. Concrete that is ready to mix
Ready-mix concrete is concrete that has been prepared and sealed in a centrally located facility. The concrete is mixed while being delivered to the location in the well-known cement trucks that are frequently seen on roads and highways. Since the cement doesn’t require any additional processing once the trucks arrive at the jobsite, it can be used right away. Ready-mix concrete is a type of specialty concrete that is mixed according to carefully thought-out specifications.
A central location where the concrete can be prepared is necessary to create ready-mix concrete. These places must be situated a variable distance away from the worksite. Concrete won’t be useful if it takes too long to get to the job site. The worksite is typically too far away from the preparation plant. Sometimes, the concrete’s setting time is accelerated by the use of retarding agents.
Because the mixture is more precisely mixed and ready to pour, ready-mix concrete is preferred over concrete mixed on-site because it minimizes confusion on the jobsite. Ready-mix concrete is useful for walls, roads, buildings, and other projects.
- 11. Concrete that Consolidates on Itself
When self-consolidating concrete is placed, its weight will cause it to compact naturally. Without the need for vibration or mechanical consolidation, this highly flowable, non-segregating concrete will fill the formwork and spread readily into place to encapsulate the reinforcement. The best uses and locations for this extremely workable concrete are those with thick reinforcement.
The following are some advantages of self-consolidated concrete:
- Self-adjusting
- Improved properties that have hardened
- Enhanced consolidation in crowded regions
- Safer place of employment
- Decreased labor and equipment
- Greater adaptability in detailing
- Softer surfaces
- Less noise
- 12. Concrete Volumetric
The issue of large distances between the concrete plant and construction sites led to the creation of this concrete as a ready-mix substitute. Volumetric mobile mixers are specialized trucks needed for this purpose. They transport the water and components for the concrete that will be combined on the building site.
When a builder needs two distinct types of concrete mix at one location, volumetric concrete comes in quite handy. One truck can produce two different mixes of concrete because the concrete can be mixed and delivered as needed. Large construction sites, basement builds, and multiple projects requiring various types of concrete can all benefit greatly from its use.
- 13. Ornamental Concrete
Concrete mixes with decorative concrete are aesthetically pleasing. Decorative concrete may undergo a number of procedures, including:
- Painting
- Forming
- Sanding
- Etching
- Adding garnishes
Any project where you want to make an artistic statement is perfect for it. It’s also a fantastic way to give plain surfaces or buildings a little “personality.” For instance, decorative concrete is a great fit for flooring and swimming pools.
- 14. Polymer-Based Concrete
In contrast to aggregates found in other types of concrete, polymer concrete aggregates are bonded together in a matrix using polymer rather than cement. Granite pebbles, quartz, silica, limestone gravels, and other materials with a high compressive strength are used to make this kind of concrete. The ability of the concrete to bind may suffer if these materials are not clean, dry, and dust-free.
The aggregate acts as the material under compressive stress, and the polymer resin acts as the binder. The composition of polymer concrete composites results in a unique combination of characteristics. Several of these attributes consist of:
- Quick-curing room temperature
- Strong adherence to surfaces
- Durability over time
- High compressive, tensile, and flexural strengths
- Poor water and some solution permeability
- Lightweight mixture
- Powerful resistance to chemicals
Additionally, polymer concrete falls into a few different categories, such as:
- Concrete impregnated with polymers
- Concrete with polymer cement
- Partially fertilized
- 15. Quick-Set Concrete
Hastily? Then quick-setting concrete is required. It works best when you don’t have enough time to finish a project. It can be used all year round because of its quicker set times and strong resistance to cold temperatures. It’s particularly helpful in the winter when the extreme cold prevents you from using a lot of other types of concrete.
- 16. Intelligent Concrete
Smart concrete is the technology for concrete of the future, as the name would imply. It is now simpler to keep an eye on the state of reinforced concrete structures thanks to the development of this kind of concrete. Short carbon fibers are added to smart concrete using a traditional concrete mixer. The concrete’s electrical resistance under stress or strain is impacted by this process. With this type of concrete, potential issues can be found before the concrete fails.
It is highly adept at identifying minute structural defects. Although it isn’t readily accessible just yet, it is anticipated to be the construction material of the future for cities that frequently experience earthquakes. Engineers in those cities can now assess the structural health of buildings following earthquakes with smart concrete, which offers a far more accurate assessment than a visual inspection.
- 17. Concrete that is Pervious
One of the most popular types of concrete for paving and constructing roads is this one. It is intended to address issues with puddles and pools of water on roads and airport runways, as well as stormwater runoff.
Water is absorbed by other concrete. Pervious concrete roads are less likely to experience hydroplaning, tire spray, and snow accumulation. It also lessens the requirement for storm sewers and curbing.
It is made up of a cement, water, and coarse aggregate mixture. Because there is no sand in it, the structure is porous and open-scaled. Water can now more readily move between the layers as a result. A few gallons of water can pass through the surface of some types of pervious concrete each minute.
- 18. Concrete in a vacuum
When poured into the formwork, concrete in some applications—like parking lots, industrial floors, and deck slabs—will contain more water than is ideal. In these situations, before the concrete sets, the excess water needs to be removed using a vacuum pump. The concrete platform or structure can be ready for use sooner thanks to the vacuum technique than with a traditional construction method.
- 19. Concrete Pumped
Pumped concrete is most likely the type of cement mixture that is utilized in the flooring of very tall buildings, if you’ve ever wondered. Pumped concrete’s secret is its extreme workability, which makes it simple to transfer via pipe to a higher level. This pipe, which releases the concrete to the needed location, will be either rigid or flexible.
Moreover, pumped concrete is useful:
- To construct superflat floors on subordinate frameworks
- In building initiatives such as roads and bridges
- For more private goods, such as swimming pools
It is frequently the only method available for placing concrete in specific areas and is a dependable, cost-effective, and efficient method of applying concrete. Pumped concrete is made with extremely fine aggregates. The concrete flows out of the pipe more freely the finer the aggregate used in the mix.
- 20. Limecrete
This concrete is made with lightweight aggregates like glass fiber or sharp sand in place of cement. It is mostly employed in the building of vaults, domes, and floors. Because limecrete is renewable and extremely easy to clean, it has numerous environmental advantages. Radiant floor heating is another application for it.
- 21. Roll-Compacted Concrete
On many American highways, one can see a large roller compacting a layer of concrete. Strong, dense concrete called roll-compacted concrete is used on busy highways with lots of heavy-duty vehicles. The production process of this concrete produces fewer emissions, which is good for the environment.
Road construction, parking lots, airport runways, pavements, and industrial servicing all use roll compacted concrete.
- 22. Glass-Crete
Glass concrete is a different, more contemporary type of concrete that uses recycled glass. When aesthetic appeal plays a significant role in the concrete’s design, this type of concrete is utilized.
This concrete, which is frequently used in large-format slabs for flooring or ornamental façades, can have glistening or colored glass embedded in it during the mixing process to give it a unique pop of color or sparkle.
- 23. Concrete Asphalt
This type of concrete, more widely referred to as “asphalt” or “blacktop,” is frequently used to build highways, parking lots, sidewalks, roads, and airport runways—basically anywhere pavement is required. The dark mineral known as asphalt is made up of bitumens, a type of hydrocarbon.
The car industry grew, and so did the demand for asphalt. Despite being well-known for its tenacity, workability, stability, resistance to skids, fatigue, flexibility, and permeability, it still needs a mixture that is properly designed. It is an asphalt and aggregate composite mixture. There are various uses for the various asphalt mixtures.
- 24. Concrete shotcrete
The application method of shotcrete sets it apart from other types of concrete. A nozzle is used to shoot shotcrete onto a formwork or frame. Compaction occurs concurrently with placing because this application necessitates higher air pressure.
Shotcrete can be used to fix steel, concrete, or wood structures that are damaged. When formwork is unfeasible or prohibitively expensive, or when access to a work area is difficult, it is also frequently utilized.
- 25. Concrete with High Strength
Any concrete mix that exceeds 40 megapascals (40MPa), the tensile strength of concrete, is considered high-strength concrete. When compared to concrete at 20 MPa or 30 MPa, high-strength concrete that satisfies this determinant can withstand substantially higher stress and pressure.
Hard conditions can be tolerated by this kind of concrete before it shears, cracks, or breaks. This concrete’s increased strength is achieved by lowering the water-to-cement ratio to a minimal level.
In civil and commercial construction, which includes buildings and infrastructure projects, structural beams, columns, load-bearing walls, and any other application where increased capacity and durability are required, high-strength concrete above 40MPa is frequently used.
- 26. Superior-Working Concrete
While all high-performance concrete (HPC) can be classified as high-strength concrete, not all high-performance concrete (HPC) falls into this category. Certain efficiency standards are met by HPC, including:
- Simple arrangement
- Hydration heat
- Environmental requirements
- Durability and longevity
- Mechanical properties over time
- Gaining strength at a young age
- Hardness
- Density and permeability factors
Nevertheless, depending on the application you intend to use it for, HPC might have limitations in some situations.