Arc Welding Steel: The Complete Guide
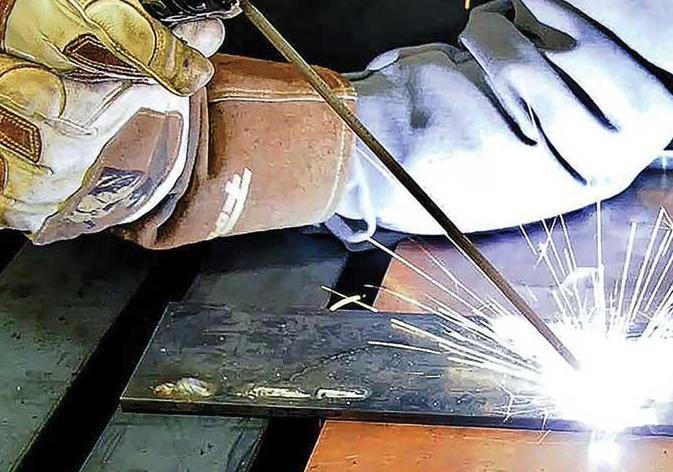
The process of welding two metal pieces together using a flux-covered electrode that melts in an electric arc and fused into the pieces is known as shielded metal arc welding. The usage of flux-coated welding rods and a straightforward transformer-style cracker box welding machine will be covered in this article.
Recognize how shielded metal arc welding works.
When a current flows through grounded metal that is being welded and across an air gap, an electric arc is created at the welding rod’s tip. The following terms and their definitions that are used in this article are:
- Machine for welding. This is the name given to the device that transforms 120–240 volts AC power into a variety of DC voltages as well as 40–70 volts AC, which is the standard welding voltage. The word “welder” refers to the person performing the welding. Typically, it consists of a big, heavy transformer, a voltage regulator circuit, an internal cooling fan, and an amperage range selector. A welder is needed to operate a welding machine.
- The welding leads, or leads. These are the insulated copper conductors that deliver low voltage, high amperage electricity to the welding work piece.
- The tool at the end of the lead that the welder uses to hold the electrode and complete the welding task is called a rod holder, sometimes known as a stinger.
- Both the ground and the ground clamp. In particular, the clamp that is fastened to the work to permit electricity to flow through the metal being welded is the lead that grounds, or completes, the electrical circuit.
- Amperage, often known as amps. This phrase, which refers to the electrical current that is given to the electrode, is electrical in nature.
- DC and reverse polarity. This alternative arrangement for arc/electrode welding provides greater versatility, particularly for applications involving overhead welding and the welding of specific alloys that are difficult to weld when exposed to AC voltages. The welding machine that generates this current is significantly more expensive than an ordinary AC welder and has a rectifier circuit or a generator for power.
- The electrodes. For particular alloys and metal types, such as cast or malleable iron, stainless or chromoly steel, aluminum, and tempered or high carbon steels, there are numerous specialized welding electrodes available. To keep the base metal from oxidizing or burning away in the arc flame during the welding process, a typical electrode is made up of a wire rod in the center covered in a special coating called flux. The flux burns as the arc is maintained, consuming oxygen and producing carbon dioxide in the weld area.
The following are a few typical electrodes and their functions:
- The mild steel E6011 electrodes have a covering of cellulose fiber. Tensile strength, expressed in pounds per square inch times 1,000, is represented by the first two digits in the electrode identification. In this case, the electrode’s yield would be 60,000 PSI.
- Electrodes with reverse polarity, known as E6010 electrodes, are frequently employed in the welding of steam and water pipes. They are especially helpful for welding overhead because the metal maintains its position during the liquid phase, as it is drawn into the molten pool by the direct current flowing from the electrode to the workpiece.
- There are other specific purpose E60XX electrodes available, but this article won’t go into detail about them because E6011s are regarded as a standard general-purpose rod and E6010s as the standard for reverse polarity DC welding.
- The low hydrogen flux coated steel rods used in E7018 electrodes have a high yield tensile strength of 70,000 PSI. These are frequently used in other applications where a strong filler material and higher strength weld are needed, such as the assembly of structural steel used in the building industry. It should be noted that while these rods offer more strength, they are less accommodating when it comes to producing a flawless, high-quality weld at the wrong amperages and with unclean (painted, galvanized, or rusted) steels. Because of all the efforts made to reduce the hydrogen content, these electrodes are referred to as low hydrogen. It is necessary to keep these electrodes in an oven set between 250 and 300 degrees Fahrenheit. At sea level, this temperature is higher than the boiling point of water, which is 212ºF. This temperature prevents the atmospheric moisture, or dew (H2O), from building up in the flux.
- Castalloy, Ni-Rod, and nickel electrodes These are unique welding rods with increased yield to accommodate the expansion and contraction of the iron material being welded. They are designed to be used for welding cast, ductile, or malleable iron.
- Dissimilar metals rods. Because they are composed of a unique alloy, these rods work better when welding steels that have been alloyed, hardened, or tempered.
- Rods made of aluminum These are more recent developments in technology that enable arc welding aluminum using a traditional welder as opposed to a specialized gas-shielded wire feed welder such as a TIG (tungsten, inert gas) or MIG (metal, inert gas) welding machine. This type of welding is sometimes called “heliarc welding,” because helium was the gas used to shield the arc flame during the process. Shielded Metal Arc Welding (stick), Gas Tungsten Arc Welding (tig), and Gas Metal Arc Welding (mig) are the official names for this arc type welding that were developed by the American Welding Society (AWS).
- Sizes of electrodes The diameter of each rod’s metal center determines the range of sizes available for electrodes. The diameter range for mild steel rods is 1/16 inch (0.2 cm) to 3/8 inch (1.0 cm), with the thickness of the material to be welded and the welder’s amperage dictating the size used. At a certain amperage range, each rod operates at its best. Selecting the correct amperage range for a given size rod will depend on the base material and the desired penetration, so specific amperages will only be covered for the welding described further in this article.
Apparatus for safety. Having the right safety gear for the job and knowing how to use it are essential components of welding safely. The following are some common supplies needed for safe welding:
- Welding shield (hood). This mask is worn to shield the welder from sparks thrown during the welding process and the bright flash of the arc. Since exposure to the arc flash can result in flash burns to the retina, standard arc welding lenses have a very dark tint. The minimum required level of darkness for arc welding is 10. It used to be preferred to use welding hoods with flip-up lenses because the dark lens could be raised, and the clear glass lens would shield the welder from slag particles as the weld was being chipped. The most sought-after welding shields on the market right now are the more recent models that self-darken. These light-colored welding shield lenses are ideal for torch cutting and grinding. The automatic self-darkening lens will switch to a pre-programmed #10 shade when it encounters an arc. The self-darkening, variable shade automatic lenses are even more recent to the market.
- Welding gloves. These are specialized leather gloves with insulation that cover the welder’s hands and lower arms, reaching approximately 6 inches (15.2 cm) above the wrists. In the unlikely event that the welder unintentionally comes into contact with the electrode, they also offer some protection against accidental shock.
- Joining leathers together. When working overhead, where sparks could ignite the welder’s clothing or result in burns, this leather jacket, resembling an apron, protects the welder’s shoulders and chest.
- Work boots. It is recommended that the person welding wear at least a 6 inch (15.2 cm) lace-up boot to protect his feet from hot slag and sparks. The insulating soles of these boots ought to be composed of a substance that is resistant to melting or burning.
Find out how to make a successful weld.
There is more to welding than just attaching two pieces of steel together by dragging a welding rod across them. The first step in the procedure is to correctly fit and fasten the work pieces, or metal that has to be welded, together. In order to completely fill the groove with a solid weld on thicker pieces, you might want to grind a bevel first. Here are the basic steps for completing a simple weld.
- Hit the curve. This is how an electric arc is formed between the workpiece and the electrode. There won’t be enough heat generated to melt and fuse metal if the electrode just lets the current flow into the grounded work piece.
- To make a bead, move the arc. In order to fill the space between the pieces that are being joined by welding, molten metal from the base metal and the melting electrode combine to form the bead.
- Form the bead of weld. In order to achieve the desired width for your finished weld bead, you weave the arc back and forth across the weld path in a figure-8 or zigzag pattern.
- During each pass, chip and brush the weld. To ensure that only clean, molten metal will be filling the weld on the next pass, you must remove the slag—that is, the melted electrode flux material—from the weld bead’s surface after each pass, or journey, from one end to the other.
- Assemble the equipment and supplies you’ll need to start welding. This includes the metal to be welded, the welding machine, electrodes, cables, and clamps.
- Prepare a secure workspace, ideally with a steel or non-flammable material table. A few mild steel pieces that are at least 3/16 inch (0.5 cm) thick will work for practice.
- Get the metal ready for welding. You might need to prepare, or weld prep, the metal if it is made up of two pieces that will be joined during the welding process. To do this, grind a beveled edge on the sides that will be joined. This permits the weld arc to penetrate far enough to melt both sides to a molten state, allowing the filler metal to bond through the metal’s sectional thickness. If possible, clean the area where the molten metal is to be worked with before beginning the welding process by scraping off any paint, grease, rust, or other impurities.
- If necessary, fasten clamps to keep your metal parts together. Locking type pliers, “C” clamps, a vice, or spring loader clamps will usually work. For unique projects, you might need to modify your methods for holding the pieces together until they are joined.
- Choose the appropriate rod and amperage range for the task at hand. For instance, an E6011, 1/8-inch (0.3-cm) electrode can be used to successfully weld 1/4-inch (0.6-cm) plate steel at 80–100 amps. Make sure the conductive material of the stinger clamp is on the clean metal at the end of the electrode before inserting it into the electrode holder, also known as the stinger.
- Switch on the welding apparatus. There ought to be a buzzing noise coming from the transformer. You might hear the cooling fan running, or you might not. Certain fans on welding machines only turn on when the machine needs to cool down. If not, you might need to examine the panel box’s breakers as well as the circuit that is supplying your electricity. The power needed to run welding machines is significant; typically, a specialized circuit rated at 60 amps or more at 240 volts is needed.
- Place the rod in such a way that it will strike the plate you are welding against as naturally as possible, and hold the stinger in your dominant hand by the insulated handle. Raise your welding shield just far enough to allow you to see clearly when advancing the electrode to just a few inches from the workpiece. Then, prepare to lower it to shield your eyes. You may want to practice tapping the electrode against the weld metal to get the feel of it before turning the power on, but never strike an electric arc without protecting your eyes.
- Decide on the starting point for your weld. After positioning the rod tip in close proximity to it, lower the welding hood into position. To complete the electrical circuit, tap the electrode tip against the metal. Then, instantly pull the electrode tip back a small distance to form an electric arc between it and the metal to be welded. Striking an arc can also be likened to striking a match. The arc gap, also known as the airspace, generates a significant amount of resistance in the electrical circuit, which is what generates the heat and arc flame or plasma required to liquefy the metal next to the weld area and the electrode.
- Press the electrode up against the metal’s surface, and when you notice an electric arc forming, gently pull it back. A continuous electric arc will form from the electrode to the work piece if you can maintain the gap between the electrode tip and the work piece. This requires a lot of practice because different electrode diameters and welding amperages call for different gap sizes. Arc gaps typically shouldn’t be bigger than electrode diameters. Start by holding the electrode 1/8 to 3/16 of an inch away from the work piece to practice steadying the arc before proceeding along the desired welding path. The metal will melt away as you move the electrode, filling the molten metal pool and creating your weld.
- Experiment with moving the electrode across the desired welding path until you can maintain a steady arc while welding at the desired speed and direction. You will practice laying, or building up, the weld bead once you have mastered controlling the arc. This is the metal deposit that forms the connection between the two parts you are welding together. The width of the gap (assuming there is one) and the depth you want the weld bead to penetrate will determine the bead-laying technique you use. In order to create a wide path, the more you weave or zigzag the electrode’s tip, the wider the bead you will lay up. The deeper the weld penetrates the metal work pieces, the slower you move the electrode.
- As you progress along the weld you are making, maintain the established arc. Jerk the stinger to free the rod from the stinger clamp or the weld metal if the electrode grounds to the metal and becomes stuck. If you move the electrode too far away from the metal’s surface and lose the arc, stop the welding process and clean the slag from the area so that there won’t be any slag in the weld area to contaminate the new weld you are starting from where the arc was lost or broken. A weak and unclean weld will result from laying a fresh bead over old slag, which will melt in the arc plasma and bubble through the new layer of metal you are applying.
- To make a wider bead, practice sweeping movements with the electrode. By doing so, you’ll be able to fill in a larger area of the weld in a single pass, producing a cleaner, stronger weld. As the electrode is drawn in a zigzag, curved, or figure eight pattern along the weld path, it is moved sideways.
- Modify the output amperage of your welder according to the material you are welding and the desired arc penetration. If you discover that the surrounding metal has simply melted or burned away, or if the completed weld bead has deep cratering at its edges, lower the amperage gradually until the issue is resolved. On the other hand, you might need to increase the amperage if you have trouble creating or maintaining an arc.
- Wipe off your completed weld. Upon completion of the welding process, you might wish to clean up your weld and remove the slag for aesthetic purposes or to improve paint adhesion. In order to get rid of any leftover slag and foreign objects, chip off the slag and wire brush the weld. Use an angle grinder to remove the top, or high portion, of the bead if the surface needs to be flat in order to fit the piece you have welded to another piece. It is simpler to inspect a clean weld to check for pitting, puddling, or other welding flaws, especially after it has been ground flat.
- To prevent corrosion, paint your weld with an appropriate rust-preventative primer. Since the base metal is directly exposed to moisture, freshly welded metal will corrode rather quickly if exposed to the elements.